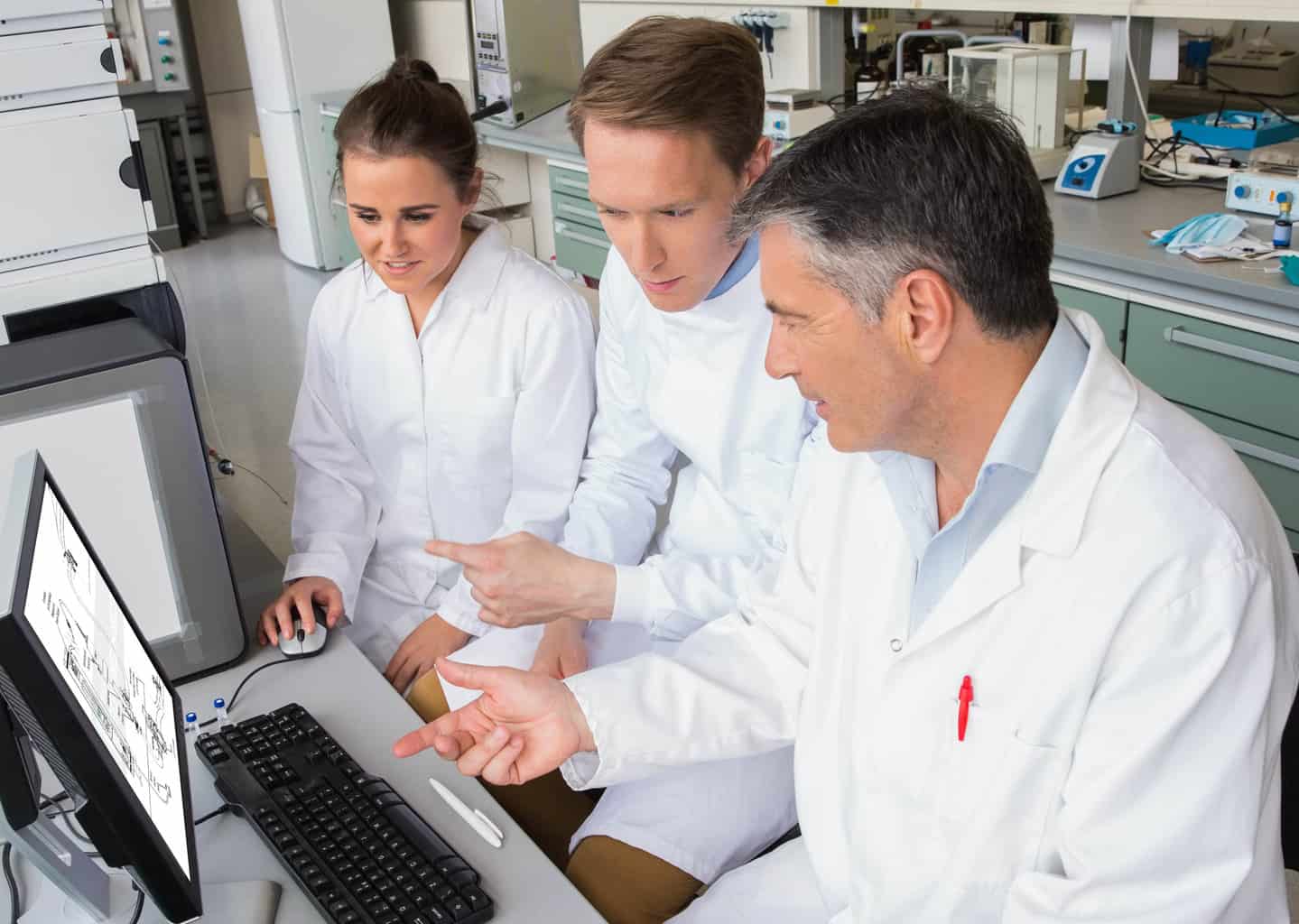
- Take advantage of our consulting services to test the feasibility, optimize and/or scale-up your ultrasonic process.
- Use our technical support services to get help with setting up and operating an ISM ultrasonic processor or a peripheral equipment set.
Overview
Consulting Services are offered to current or prospective customers looking for help with evaluating the feasibility, optimizing and/or scaling up their ultrasonic process. These services are provided at ISM facilities or remotely (e.g., by video conferencing or telephone). Please be advised that ISM does not work with materials that may be hazardous to health, possess a strong smell or are illegal in the State of Florida.
Warranty Support is included with a sale or lease of any ISM ultrasonic processor to make sure it runs as specified (i.e., produces the expected ultrasonic amplitude, power, and frequency output). Technical support services are telephone/email/video-conferencing time, which are also available to customers who need help with setting up, operating and maintaining ISM ultrasonic and peripheral equipment. To contact our technical support team or open a support ticket, please use the Contact Us link below.