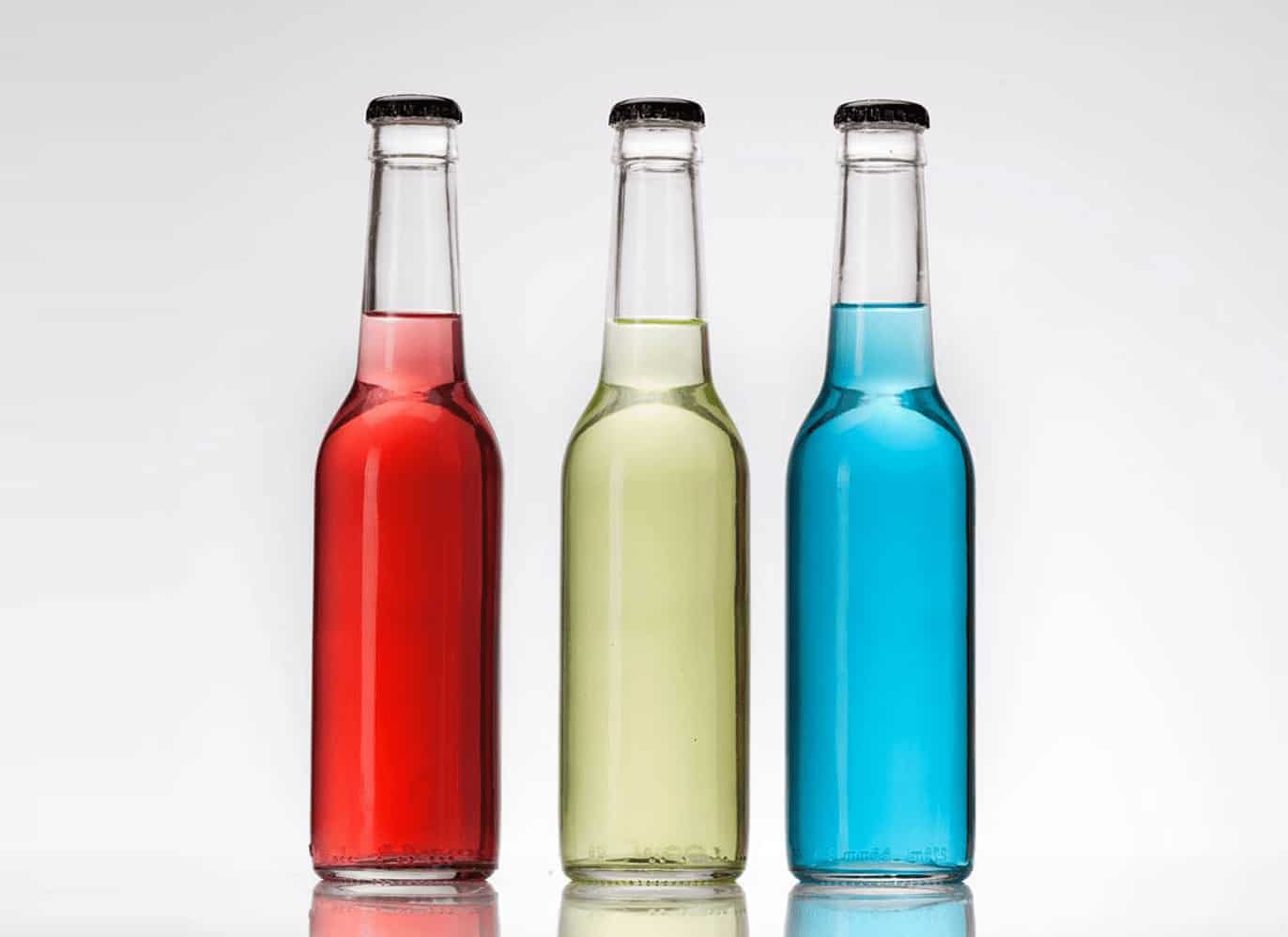
- Convert water-insoluble ingredients into liquid or powdered nano-formulations, ensuring complete solubility in water, extended shelf life, increased bioavailability and shortened onset of action.
- Infuse food and beverage products with nano-formulated vitamins, cannabinoids, alkaloids, terpenes and many other compounds.
- Extract ingredients from plants and mushrooms, achieving superior yields and rates while using greener alternatives to harsh organic solvents.
Overview
Until recently, the use of lipophilic ingredients (oil-soluble vitamins, alkaloids, cannabinoids, terpenes, coenzymes, phytosterols, carotenoids, flavonoids, curcuminoids, phenolics, polyunsaturated lipids, etc.) in food and beverage products has been restricted by technological challenges. Since these compounds are not water-soluble, they cannot be incorporated into water-based beverages by simple infusion and are known to exhibit very low bioavailability profiles. These challenges can now be overcome by converting lipophilic bioactive ingredients into fully water-soluble liquid or powdered nano-formulations. These products are kinetically stable, highly bioavailable, and fully water-compatible: they can be readily infused into food and beverage products without compromising their shelf-stability and ensuring that the bioactives are absorbed by the body rapidly and completely. Nano-formulations with droplet diameters well below 100 nm are translucent and become transparent when diluted with water, so they do not alter the appearance of beverages even when very strong doses are infused.
Furthermore, Industrial Sonomechanics’® technology is capable of extracting a diverse variety of ingredients from plants, mushrooms, and other substrates, providing superior yields and processing rates. Our technology also makes it possible to substitute harsh and unsafe organic solvents with much milder and greener alternatives. Additionally, Industrial Sonomechanics’® equipment can be used to degas beverages and sauces by removing entrained air bubbles and dissolved gases from a variety of liquids.
Overall, Industrial Sonomechanics’® laboratory, bench, and industrial ultrasonic liquid processors provide significant benefits to the food and beverage industry, from improving the solubility of hard-to-dissolve ingredients to extracting valuable compounds while ensuring product safety, to degassing finished products.
Furthermore, Industrial Sonomechanics’® technology is capable of extracting a diverse variety of ingredients from plants, mushrooms, and other substrates, providing superior yields and processing rates. Our technology also makes it possible to substitute harsh and unsafe organic solvents with much milder and greener alternatives. Additionally, Industrial Sonomechanics’® equipment can be used to degas beverages and sauces by removing entrained air bubbles and dissolved gases from a variety of liquids.
Overall, Industrial Sonomechanics’® laboratory, bench, and industrial ultrasonic liquid processors provide significant benefits to the food and beverage industry, from improving the solubility of hard-to-dissolve ingredients to extracting valuable compounds while ensuring product safety, to degassing finished products.
Case Studies & Application Reports
All-Natural CBD Extract Nanoemulsion
Nanoemulsions for Food and Beverage
Beverage Sterilization/Pasteurization
Ultrasonic Degassing of Food and Beverages
Blog Posts
07/28/21
Webinar Recording & Q&As: Water-Compatible Nanoemulsions: The Battle of Formulations
In March of this year, Industrial Sonomechanics (ISM) hosted a webin... Read more...
03/31/18
Chapter Published in a New Book on Ultrasonic Food Processing
Industrial Sonomechanics (ISM) is pleased to announce the recent pub... Read more...
04/16/16
Ultrasonic Pasteurization of Milk and Water-Based Beverages
One of the main challenges in the food & beverage industry is the in... Read more...
Customer Testimonials
Khara Cartagena, Cannabis and Hemp Productions
“We recently purchased a BSP-1200 system from ISM and were very impressed with its performance. The word got out, and one of our customers came to our facility to perform CBD-oil emulsion tests with the system. Though he was initially skeptical, after running the machine for only 1 min he got far better results to what he was able to achieve in over an hour with his conventional ultrasonic processor. He absolutely loved the BSP-1200 and bought it off from us that same day to take to his facility in CA! We have now decided to go straight for ISM’s production-scale ISP-3000 processor.”